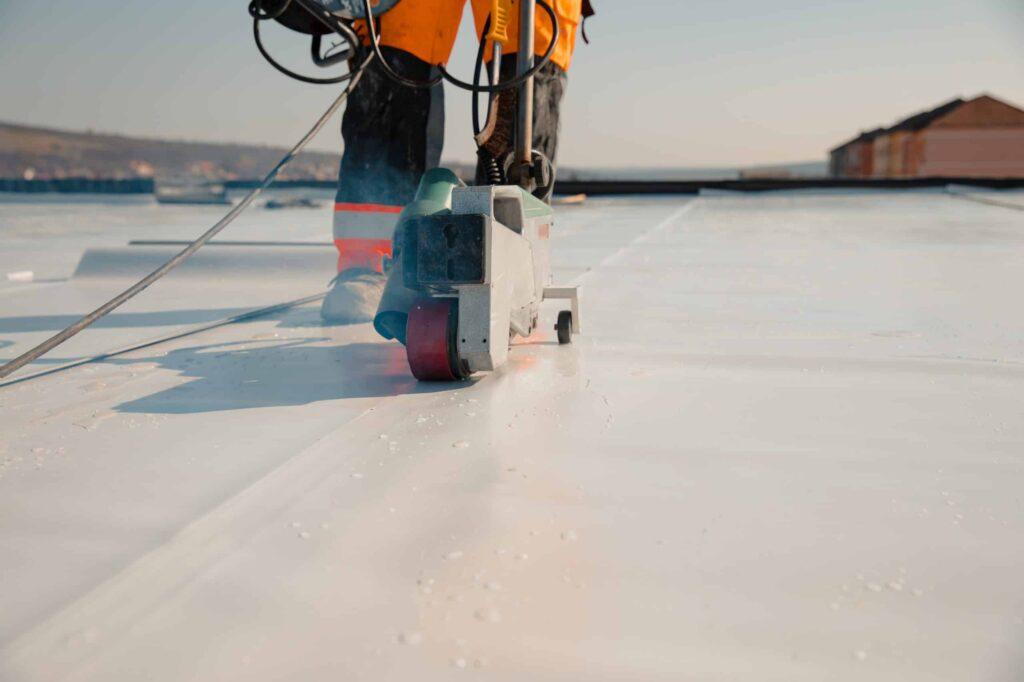
Expert Installation and Long-lasting Protection
Spray foam roofing offers a modern solution for building protection in Southern Illinois. ArmorGuard’s professional spray polyurethane foam (SPF) roofing systems create a seamless, fully-adhered barrier that prevents leaks while providing superior insulation and durability.
We specialize in careful evaluation and preparation of roof surfaces before applying the precise thickness of spray foam needed for optimal performance. Our trained applicators understand the intricacies of spray equipment, foam materials, and industry best practices to deliver lasting results.
At ArmorGuard, we prioritize taking care of our customers through expert installation and maintenance services. The energy efficiency and moisture resistance of our spray foam systems help property owners in Southern Illinois protect their investments while reducing heating and cooling costs.
Benefits of ArmorGuard Spray Foam for Roofing
ArmorGuard’s spray foam roofing system delivers superior insulation, exceptional durability, and streamlined installation to protect and enhance your property’s performance.
Energy Efficiency Enhancements
Our spray foam roofing creates an airtight seal with exceptional R-value properties that significantly reduce heating and cooling costs. The foam’s closed-cell structure prevents air leakage and thermal transfer through the roof.
Tests show buildings with spray foam roofing can achieve up to 30% reduction in energy consumption compared to traditional roofing systems.
The insulation maintains its performance long-term without settling or degrading, providing consistent temperature control year-round.
Durability and Lifespan
Our spray foam roofing forms a monolithic barrier resistant to wind, rain, and UV exposure. The seamless membrane eliminates weak points where damage typically occurs.
The material’s flexibility allows it to expand and contract with building movement without cracking or separating.
With proper maintenance, our spray foam roofs last 20-25 years before requiring recoating, substantially longer than conventional roofing materials.
Seamless and Lightweight Application
We apply the foam as a liquid that expands to create a perfectly contoured surface, conforming to any roof shape or obstacle.
The foam’s lightweight nature adds minimal structural load while providing excellent strength. At just 0.5 pounds per square foot, it’s ideal for both new construction and retrofits.
Installation requires no seams, joints, or mechanical fasteners that could fail over time. The foam adheres directly to most existing roof surfaces after proper preparation.
Installing Spray Foam in Southern Illinois
Proper spray foam roofing installation in Southern Illinois requires careful attention to weather conditions, thorough site preparation, and skilled application techniques by certified professionals.
Climate Considerations
Southern Illinois experiences hot summers and cold winters with frequent temperature swings. We carefully monitor weather forecasts and humidity levels before scheduling installations.
The ideal temperature range for spray foam application is between 50-90°F. Spring and fall often provide the most consistent conditions.
We adjust our application techniques based on seasonal challenges. In summer, we schedule early morning installations to avoid extreme heat. During cooler months, we use specialized heating equipment to maintain optimal material temperatures.
Site Preparation and Safety
Our team thoroughly cleans and inspects all roof surfaces before installation. We remove debris, repair damaged areas, and address any moisture issues.
Essential Safety Measures:
- Setting up fall protection systems
- Establishing controlled access zones
- Installing warning lines and safety barriers
- Ensuring proper ventilation
The substrate must be completely dry. We use moisture meters to verify conditions meet manufacturer specifications.
Professional Installation Process
We apply spray foam in multiple passes to achieve the specified thickness. Each pass is typically 0.5 to 1.5 inches deep.
Quality Control Steps:
- Continuous thickness measurements
- Regular adhesion testing
- Documentation of ambient conditions
- Visual inspection of foam pattern
A protective UV-resistant coating is applied once the foam cures. The coating color is selected based on energy efficiency goals and building requirements.
We maintain strict quality control throughout the process, including equipment calibration and material temperature monitoring.
Why Choose Us for Spray Foam Roofing?
Superior Energy Efficiency
Leak & Moisture Protection
Durable & Long-Lasting
Seamless & Lightweight Application
OUR WORK
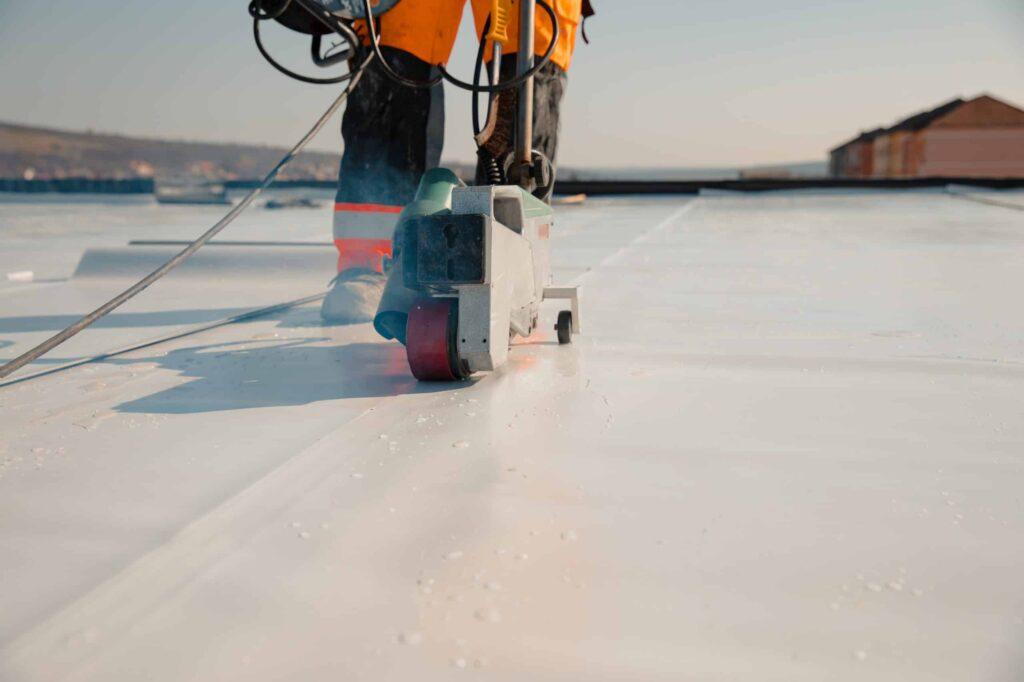
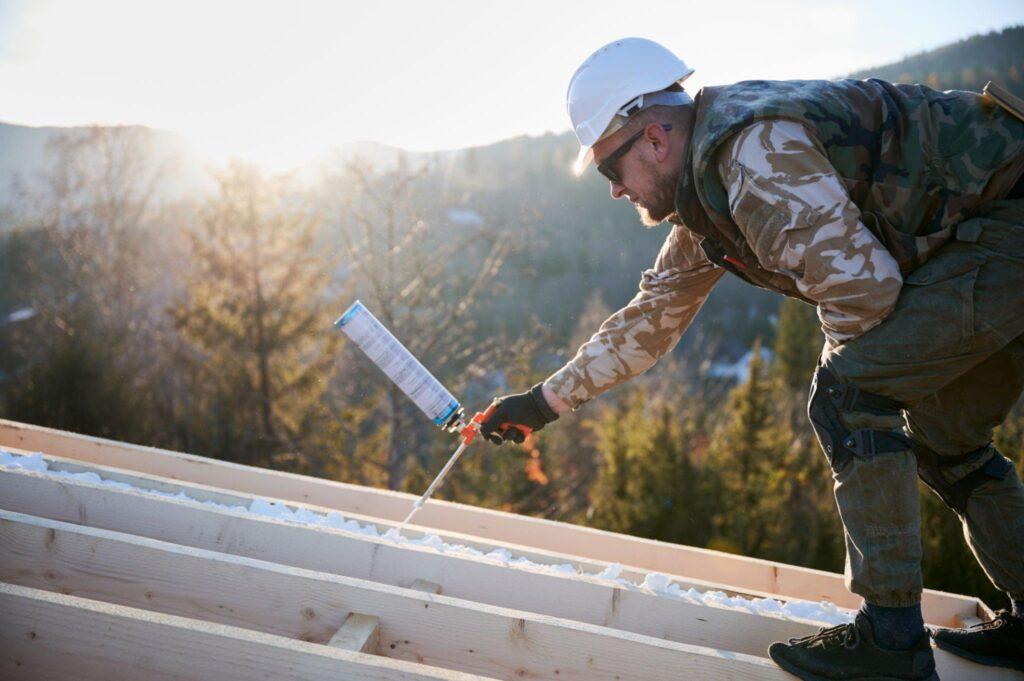
FREQUENTLY ASKED QUESTIONS
Spray foam roofing creates a seamless, monolithic barrier that effectively resists wind uplift and prevents water penetration. The material maintains its structural integrity in temperatures ranging from -50°F to 180°F.
The foam’s strong adhesion to the substrate prevents delamination during severe storms and high winds.
A properly installed and maintained spray foam roof can last 25-30 years. The protective elastomeric coating can be reapplied periodically to extend the roof’s service life.
The underlying foam material retains its insulating properties and structural integrity throughout its lifespan.
We recommend bi-annual inspections to check for any coating wear or physical damage. The roof surface should be kept clear of debris and standing water.
Regular recoating is needed every 10-15 years to maintain UV protection and waterproofing capabilities.
Spray foam provides continuous insulation with an R-value of 6.5 per inch of thickness. This seamless barrier eliminates thermal bridges and air leakage points.
Buildings with spray foam roofing typically see 20-30% reductions in heating and cooling costs.
Professional installers must wear appropriate personal protective equipment including respirators, protective clothing, and eye protection. The installation area requires proper ventilation and restricted access during application.
Building occupants should vacate the premises during installation and return only after the required re-entry period.
Small punctures or damage can be easily repaired by cutting out the affected area and applying new foam material. The seamless nature of spray foam allows repairs to blend perfectly with the existing roof surface.
Most repairs can be completed in a few hours with minimal disruption to building operations.